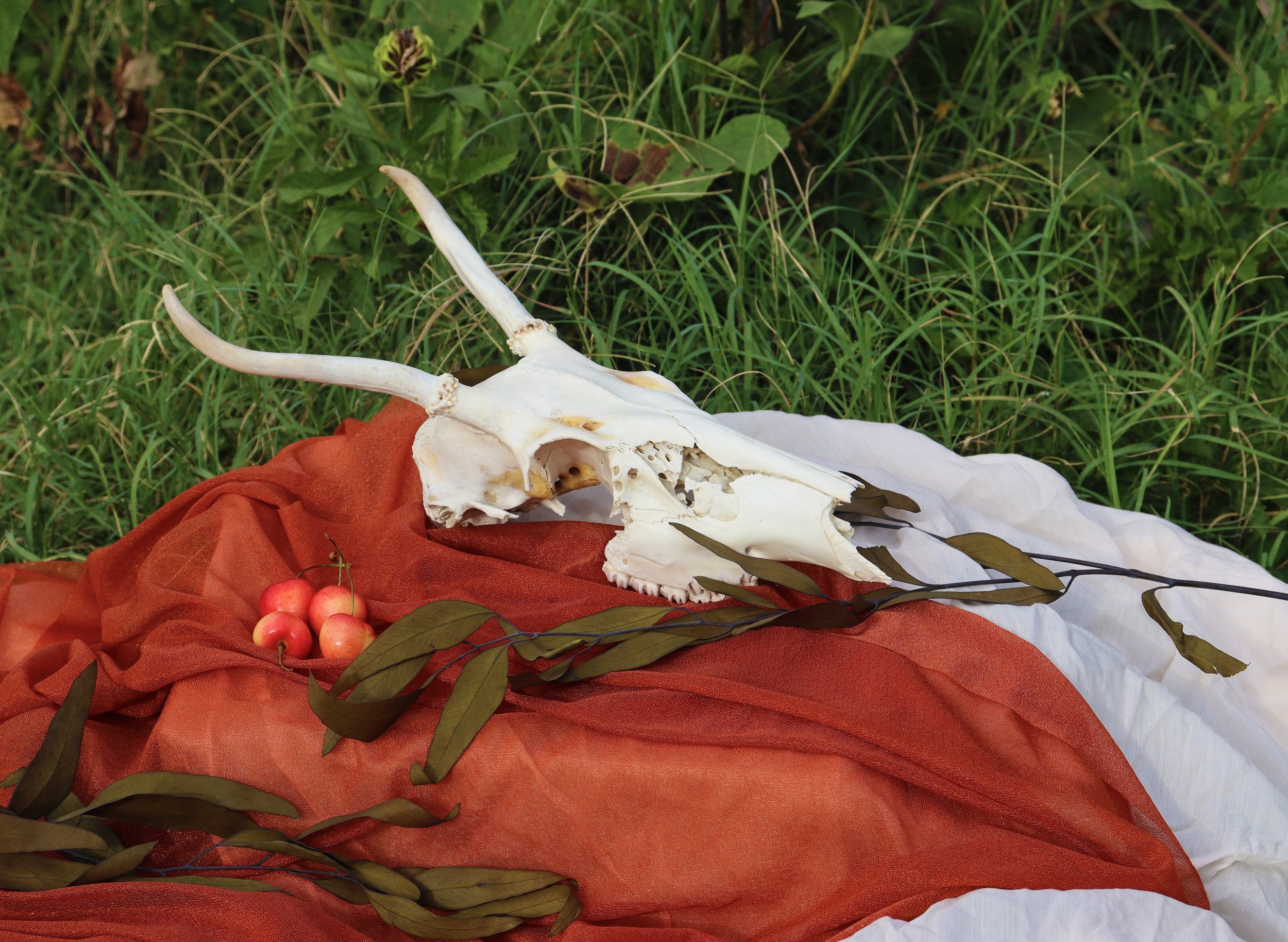
The Production Process and Our Experience as First Time Designers
The production process has long been shrouded in mystery; it’s alway been who you know and trust your connections. Manufacturers tend to work with experienced designers who have been in the industry for years before they begin their own line, and this can lead to an intimidating trial and error process for first time designers looking to have their own line from the start. As designers who had only ever made our garments by hand on home sewing machines, we had some hiccups along the way to our production. As we move forward, we want to pull back the curtain on manufacturing and give a little insight on the best way to get your line going.
Now that you have a pattern, a sample can be made. You want the manufacturer who will be doing your production to produce a sample. That way, you can see the quality of their work - the stitching, the finishes, if seams line up. You can also test the official fit of the garment with the sample, fitting on a fit model, or yourself. From here, edits are made. If the garment needs to be changed in anyway now that you’re seeing it fully made, those changes are communicated to the pattern maker and manufacturer so your inventory can come out exactly the way you want.
All this information is kept track of in a Tech Pack. This is a series of documents that is complied throughout the production process that contains everything there is to know about the garment. This includes the Flat, fabric samples, measurements, closure samples (like zippers or buttons), notes about stitches, a cut list, and more. If you decide to hire a Technical Designer, they can help you assemble and update the Tech Pack, as well as help you determine how much fabric you’ll need, and assist in pattern adjustments.
Edits are completed, you love your design, and it’s time to move on to full production. If you’re offering your design in more than one size, your pattern will need to be graded to each size for production, and you’ll want to get a size run produced to check fit through all your sizes and make sure the quality of construction remains consistent. From there, the manufacture will take the Tech Pack, the patterns, and any other information you provide, and go into full scale production of your line.
Every design begins with a fashion sketch. This is your illustration of what the garment looks like - your idea. However, this is usually very artistic and doesn’t communicate the construction aspects of the design. The sketch needs to be translated into a Flat. A Flat Sketch is a line rendering of the garment, and illustrates the technical part of the design. This includes all the seams, darts, pleats, closures, stitching, embroidery, pockets, etc. This can be used by pattern makers and technical designers to construct our garment.
With the Flat, your pattern can be drafted. You can hire a pattern maker to do this for you, or draft it yourself. The pattern is the map of the garment, and will be used all the way through the production process. Pattern Makers can be expensive, so be sure you’re hiring the right person for your needs. Technical Designers can also be helpful during this time. If you aren’t familiar with fitting techniques or what goes into constructing a garment, hiring a Technical Designer can be helpful in deciding what your garment needs to meet your vision.
The Process
Tarot was our first full scale manufactured line. We wanted to make styles for everyone - so they could express themselves no matter the event or venue. This was a tall order for a beginning experience. Armed with our fashion degrees, we had hoped for this to be an educational journey we’d be taking with our manufacturer. This is not what happened.
While Tarot is beautiful in how it ended up being developed, this was not the original vision, and these changes had to be made because we were left in the dark for the majority of the process and ran into more complications than we anticipated. It’s important to find the manufacturer that is right for you, but if you don’t know what you need, it’s easy to be taken advantage of. We under estimated costs, we were misquoted on both cost and timeline, we were left out of a lot of the decision making, and communication was neglected. Here are some things we would recommend to avoid what we went through.
Try to do as much as you can yourself. Not only will this cut down on costs, this will keep you more involved in the whole process. In our case, our manufacturer also did our preproduction (pattern making, fabric sourcing, and Tech Packs). If you can take on any of this yourself, especially the pattern making, you’ll be able to save a ton on cost and have more control over how things come out.
Really shop around for a manufacturer and check reviews. This is hard to do, since most manufacturers don’t have a Yelp page. But the BBB and other sites like that can really help in determining who is a good fit for you. Look at their past portfolio. Are they really good with children’s wear? Do they exclusively work with leather? Are there brands you like that they’ve worked with in the past? Get a quote. Is it in your budget? Make sure you secure a contract that details everything they’ll be doing for you, how much it’s going to cost, and any thing that might change as you work together. Don’t fall for the sales pitch - compare pros and cons.
Try to keep a realistic timeline. When we started, we were told Tarot would take anywhere from 6-8 months to complete from sketch to inventory. If you have a large project, start looking for a manufacturer early. We began looking in September and were told to expect a May delivery. They may also have a packed schedule; the manufacturer you want and fits your project might not be able to take it on within your timeline for launch.
Our Experience
The fashion industry is a place of expression and glamor, but it is an industry just like any other. This comes with all the money, contacts, steps, and connections that make the product world go round. We hope our experience with our first line will help you navigate the production process a little easier. Keep in mind, it doesn’t have to be perfect the first time. Patterns might take five tries. Fitting might require six mock-ups. Your design might change eight times before you’re satisfied. Perfect comes when the style makes you feel like yourself. And we can’t wait to see what you come up with.